Rethinking HVACR Maintenance: The Imperative change of Business-as-Usual
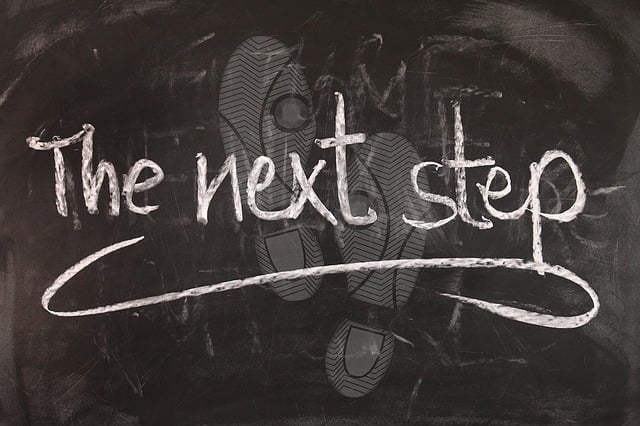
In the Heat pump and cooling industry, traditional ‘business-as-usual’ (BAU) practices have reigned supreme for decades. In an era where technology rapidly evolves and the focus on sustainability rapidly increases, it’s clear that traditional “BAU” approaches are no longer sufficient.
The Downside of Business-as-Usual
Business-as-usual in HVACR maintenance generally leans towards a schedule based (preventive) and/or reactive approach, that involves repairing and servicing equipment only after a problem has presented itself. Although such practices might initially seem cost-effective, they’re fraught with pitfalls that can compound over time.
First, there’s the issue of unplanned downtime. Equipment failures aren’t scheduled and can lead to significant operational disruption, hampering productivity and compromising the comfort of a building’s occupants.
Second, there are the financial implications. While BAU maintenance can save on upfront servicing costs, it often culminates in substantial repair expenditures when systems fail unexpectedly. Emergency repairs can be considerably costlier than routine maintenance, with additional expenses incurred due to urgency or escalated damage caused by deferred action.
Third, equipment lifespan can be drastically reduced. HVACR systems that aren’t regularly maintained may succumb to more severe issues, necessitating more frequent replacements and resulting in higher capital expenditure.
Lastly, BAU maintenance can lead to inefficient operation, higher energy use, greater carbon emissions, and larger utility bills. Moreover, HVACR failures can potentially pose health and safety risks, including extreme temperature conditions, poor air quality, and even mold growth.
The Promise of Predictive Maintenance
Given these downsides, it’s evident that an alternative approach is necessary. This is where predictive maintenance comes into play, offering significant improvements in several key areas.
Predictive maintenance minimizes downtime. By continually monitoring equipment performance and predicting potential failures, it allows for planned repairs that can be scheduled to cause the least disruption.
The approach offers substantial cost savings in the long run. Predictive maintenance might involve higher upfront costs, but it pays for itself by averting costly emergency repairs, reducing energy consumption, and extending equipment life.
Predictive maintenance ensures that HVACR systems operate at their highest efficiency, which in turn reduces energy use and CO2 emissions. It also prevents HVACR failures, thus maintaining a comfortable and safe environment within the building.
Moreover, predictive maintenance provides a clear understanding of equipment condition and performance over time, enabling better planning for capital expenditures and budgeting.
The Risk of Not Adapting
For those companies hesitant to make the shift from “BAU” to predictive maintenance, consider the cautionary tales of those who failed to adapt to changing times.
Kodak, for instance, clung to its film business, despite recognizing the potential of digital photography early on. As a result, it lost significant market share and filed for bankruptcy in 2012. Similarly, Blockbuster didn’t adapt to the rise of digital streaming platforms, leading to its downfall.
In the HVACR industry, the failure to shift from BAU to predictive maintenance can lead to similar outcomes, both for service providers and equipment owners (e.g. property owners). As a HVACR system often are business critical, a breakdown will force both parties to focus on a “unnecessary problem” rather den business development. Add the increasing focus on energy efficiency and sustainability, companies that stick with inefficient, outdated maintenance practices risk being left behind.
In summary, the shift from BAU to predictive maintenance represents a significant advancement for anyone utilizing it, both service suppliers as well as companies implementing it as the main form of maintenance. While the transition may require a cultural shift within organizations, it’s crucial for achieving sustainable, long-term gains.
For the sake of operational efficiency, cost-effectiveness, and sustainability, the HVACR industry must embrace this change.
The guide
We have prepared a guide to help as well as accelerate the transformation which can be downloaded here
More news
ClimaCheck online – Maintenance – 6-7/7
During this weekend (sixth and seventh of July), ClimaCheck online will be through some planned maintenance.
HVACR optimisation and the potential reduction of CO2!
Multiple organisations have evaluated the saving potential within HVACR optimisation, and reached similar conclusions: it is possible to reduce CO2 emissions by millions of tons by optimising HVACR systems.
Midsummer celebration and information on our office hours for the Summer!
This special time of year brings us together to enjoy the light, dance around the Maypole, and welcome the summer!