System Efficiency Index – The Game Changer
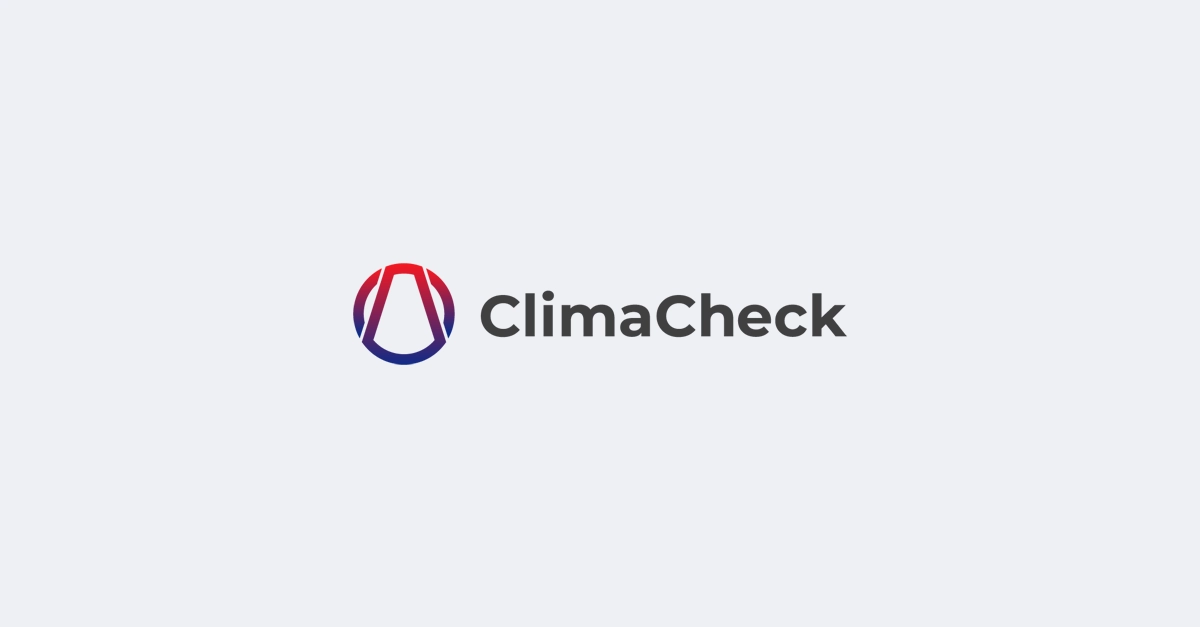
Author – Klas Berglöf, Founder of ClimaCheck Sweden AB
35 years ago I started to work with air conditioning, heat pumps and refrigeration (HVACR). Performance was rarely measured and when it was, the common method was to use a flow meter and measure temperature differences to calculate the cooling capacity and from that calculate COP. This method is still common practise.
The limitations of the method, and lack of information it provides, makes it time consuming and inefficient to identify what causes efficiency deviations. Any small error in measurements would also render it totally invalid.
Flow meters are costly to apply and only work on water-based circuits in the field. With such challenges in flow measurement, small temperature differences and unstable systems, it is impractical to use flow meters accurately in the field.
To counter this, I developed a unique method based on fundamental energy laws and accurate refrigerant fluid data to closely measure HVACR system performance, giving all the answers directly. So, we could now identify problems more quickly and accurately, thus knowing what to do to prevent performance drift. We could therefore fix systems quickly with less downtime for customers. This technique is today known as the “ClimaCheck Method”.
However, the HVACR-industry has not changed much, over the last 35 years, when it comes to maintenance. It is still “business as usual”. This has created a peculiar situation, where proactive equipment owners start to demand accurate performance data and reports for their HVACR equipment from unaware maintenance contractors. They want to ensure they are achieving the efficiency and performance they have paid for to meet environmental regulations. ClimaCheck measurements enable them to make huge savings via measurement-based optimisation and early detection of efficiency deviations.
Climate change is predicted to cause more frequent hot and cold weather extremes, increasing stress on HVACR systems. This is generating a strong demand for predictive maintenance. The market will not accept failures because it is a hot day!
It’s time to change!
I have said this before, but it is worth mentioning again; Almost all failures can be detected long before the symptoms are evident, but very few are noticed. So, why are so many systems still running themselves to failure? I would argue that this is a result of “business as usual” and unclear responsibilities, this causes ‘finger pointing’ to avoid responsibility, coupled with an unwillingness to adopt new technologies and methods.
Coefficient of Performance (COP), Energy Efficiency Ratio (EER) or kW/RT have been used as indicators of good performance for a long time. But COP/EER or kW/RT change continuously with operating conditions and must be related to specific parameters such as outdoor temperature, cooling water, chilled water temperature, flow rates, cooling capacity, etc. So, these are only useful for a refrigeration expert with a lot of time to spend on analysis work.
Meaningful conclusions can only be drawn after a careful evaluation of operating conditions and mean nothing to people without a degree in thermodynamics and long experience. To be honest, monitoring COP or kW/RT has a very limited impact on performance, failures or down-time.
Time is expensive and most organisations that demand COP/EER values do not have the resources / time / expertise necessary to decide whether a COP value is good or bad and even less so to identify what the cause of poor performance might be. This is often overlooked, but there is a great solution – SEI.
System Efficiency Index (SEI)
SEI overcomes the challenges of COP/EER and efficiency measured in kW/RT, these are dependant on operating conditions, where science is required to know whether a value is “good” or “bad”. SEI always reflects good or bad system efficiency and a SEI of 50% will always be a very efficient system! This makes it easy for anyone to see if a Water Chiller, Heat Pump or any type of Refrigeration System is performing well under the current conditions. If the SEI is lower than expected, the SEI Sub-Efficiencies will show where losses are occurring (compressor, evaporator, condenser, etc.) and thus indicate what needs to be done to fix the problem. These answers cannot be given by secondary flow-based measurements.
How SEI Works.
SEI was developed within different projects by the Institute of Refrigeration (IoR) in UK, The Mechanical Engineering Industry Association (VDMA) in Germany and ClimaCheck in Sweden. In 2013-2014, a Swedish research project (financed by the Swedish Energy Agency and operated by the Swedish National Test Institute, RISE/SP), evaluated the earlier work and adapted SEI for HVACR field measurements. The earlier work by IoR/VDMA had defined SEI mainly as a tool for efficient design. The key point here is that field measurements can now verify the intended design performance under real operating conditions.
The key performance indicator today is System Efficiency Index. SEI is the efficiency barometer for every refrigeration, air-conditioning or heat pump system as compared to a 100 % efficient (loss free) system at the same operating conditions, when measured. The ideal loss-free process is defined as the “Carnot Efficiency” based on using the “reference temperatures” relevant for the system being analysed.
These “reference temperatures” must be defined with care to correctly reflect the performance of different applications. With correctly defined “reference temperatures”, the “Carnot COP” is the ideal process at these conditions.
The use of SEI and Sub-Efficiencies in daily work
Working with SEI and Sub-Efficiencies makes it easy to interpret a wide range of operating conditions and decide what action to take.
Using SEI and Sub-Efficiencies to analyse true performance during maintenance, makes it possible to instantly see if any component has a problem, thus reducing time consuming and costly troubleshooting (This is where I started 35 years ago!). Corrective actions can be taken before issues cause major problems or failure. By optimising system efficiency – power consumption and running costs are reduced substantially, whilst system reliability and lifetime are increased.
When SEI and Sub-Efficiencies are monitored 24/7, the right person gets the right information in time to plan corrective actions to fix the problems. Thus avoiding expensive failures and down-time. After the job is done, the performance is verified and documented automatically if analysing performance with ClimaCheck.
What happens now?
Keeping the desired temperature is not enough. Systems need to be efficient. I often see energy savings of more than 20% in systems that consume 30-60% of a buildings total energy consumption.
Since I started working with performance analysis, the market has changed drastically. More companies now understand the potential benefits by accurately analysing performance and efficiency. If equipment owners know that it’s possible to avoid problems and failures, it is not an option to run a system to failure, with increased maintenance costs, destroyed food, or unhappy tenants as a result.
During the last year I have seen an increased realisation and interest among companies that understand the benefits of energy efficiency, predictive maintenance, Measuring and Verification (M&V) and Fault Detection and Diagnostics (FDD). SEI is already and will increasingly become a crucial tool to ensure energy efficiency in the HVACR industry! With SEI and Sub-Efficiencies information available, it is now possible to precisely optimise and ensure the best energy efficiency within all refrigeration processes!
More news
World Refrigeration Day 2025 – Technology, Climate Action and an Industry Progressing into the Future.
June 26th marks World Refrigeration Day, a day to recognise the technology that enables life as we know it.
Office Hours During Midsummer Celebrations and the Summer
We wish you a joyful Midsummer celebration filled with happiness
New Employee, the ClimaCheck network is growing!
Say hello to Julian Schoch our new COO! Speaking German, English and Swedish, he’ll be a familiar face (and voice) to many of you in our daily communication.